- Your current location: Home >> Product >> Molding equipment
- molding equipment Casting sand treatment equipment Accessory description Picture of clay sand mold Casting pictures Qualification certificate
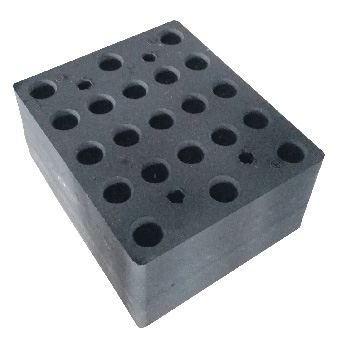
The horizontal tidal sand molding machine is suitable for producing small batches and relatively complex castings. The horizontal parting is convenient to place the coated sand core head. The operation mode is diversified and can be flexibly selected according to the needs and workshop space. It is suitable for the molding production of small and medium-sized casting enterprises, instead of the traditional artificial casting molding. The molding speed of conventional equipment can mold about 60-120 sand molds per hour under the conditions of meeting the operation.
- 01.
Conventional horizontal parting molding machine for tidal sand
A conventional horizontal single-shot sand injection molding machine developed for small and medium-sized casting enterprises is very suitable for upgrading manual molding or shock-pressure molding to automatic molding, improving the production efficiency of castings and the control of finished products.
1) Size range of sand box: 420mm - 710mm;total height of sand mold 400mm (200mm+200mm);
2) Air pressure sand blasting and hydraulic compaction;
which is suitable for the production of small and medium-sized castings with relatively simple shape; 3) The molding speed is 90 molds per hour (excluding the placement of coated sand cores);
4) The molding speed is 90-110 molds per hour (without placing clay core);
Reading >>
- 02.
Lower sand box slides out of horizontal parting molding machine
In the lower sand box of the molding machine, we adopt a slide-out (drawer type) design, which is convenient for operators to accurately and easily place the coated sand core head, such as casting molding of valves, pipe fittings, brake discs, etc. It also improves the safety of the operator to a certain extent, and we also ensure the accuracy of mold closing and the durability of the machine in the design of the mechanical structure;
1) Size range of sand box: 420mm - 1200mm;total height of sand mold 520mm (260mm+260mm)
2) The upper and lower oil cylinders are squeezed against each other;
3) Selectively let the lower sand box slide out or close the slide out;
4) There is more space to place the coated sand core;
5) The molding speed is 70-85 molds per hour (no clay core is placed);
Reading >>
- 03.
Horizontal parting molding machine with top and bottom sand shooting
The top and bottom separate sand shooting machines are used to make the sand filling method closer to manual molding, so that more complex or large concave-convex castings can make perfect sand mold through the molding machine. This machine is also a derivative of conventional machines and has been widely recognized and used in recent years.
1) Size range of sand box: 420mm - 900mm;
2) Make the sand fill more evenly and tightly;
3) The coverage of casting production molding is more extensive;
4) The total height of sand mold is 600mm (300mm+300mm);
5) Molding speed 80-95 moulds per hour (no clay core);
Reading >>
- 04.
Large size sand casting automatic molding machine
The large size horizontal molding machine developed according to the molding requirements of the foundry enterprises adopts two vertical sand shooting barrels designed to shoot sand on both sides to meet the casting molding of some large castings, such as manhole covers, sewer grates, piano supports, etc. At present, the largest sand box size is 1600mm x 1400mm, and has been put into normal production molding.
1) Size range of sand box:1000mm - 1600mm;
2) Double-sided sand blasting filling;
3) Suitable for automatic casting modeling of large castings; 4) Molding speed 40-50 moulds per hour (no clay core);
Reading >>
- 05.
Tidal sand horizontal molding production line
This is a complete set of automatic horizontal parting molding production line of wet sand. The automatic horizontal molding machine is equipped with a conveyor car and automatic placement of box frame and weight iron. The molding and pouring are carried out at the same time, and the poured sand mold is automatically transported into the cooling area. Finally, the sand is separated from the casting, so that the old casting sand is automatically collected into the sand treatment system.
1) Automatic placement of sand box frame and ballast iron;
2) Automatic molding and pouring are carried out at the same time;
3) Small footprint, clean operation environment and the highest degree of automation;
4) Can be matched with automatic pouring equipment;
Reading >>
- 06.
Crawler transmission horizontal casting production line
A crawler-type horizontal casting production line used to carry the drive casting sand mold. The casting is also in progress when the molding machine is molding. It is normally matched with two production lines A and B, one for casting and the other for cooling. The cooled sand mold enters the high-temperature resistant belt and finally reaches the shakeout machine. Its main function is to replace manual transfer of sand mold and keep the workshop clean and tidy.
1) Replacing manual transfer of casting sand mold;
2) Make the foundry more clean and tidy;
3) Suitable for castings with light weight, short cooling time and no need to place box frame and heavy iron;
Reading >>
- 07.
Drive pouring line of track support plate
This is a track transmission line to avoid automatic molding and pouring at the same time, and it also reserves the labor costs of manual transfer of sand mold and other labor. Compared with many foundry enterprises, they choose this casting production line in order to save electricity costs and stagger the peak period of electricity consumption. However, the degree of automation is not ideal, which requires manual placement of sand box frame and covers more workshop area.
1) Avoid automatic molding and pouring at the same time;
2) It can realize automatic transmission to place the sand mold, but it is necessary to manually place the sand box frame and the weight iron;
3) It occupies more workshop area, but all casting sand molds can be poured at the same time;
Reading >>